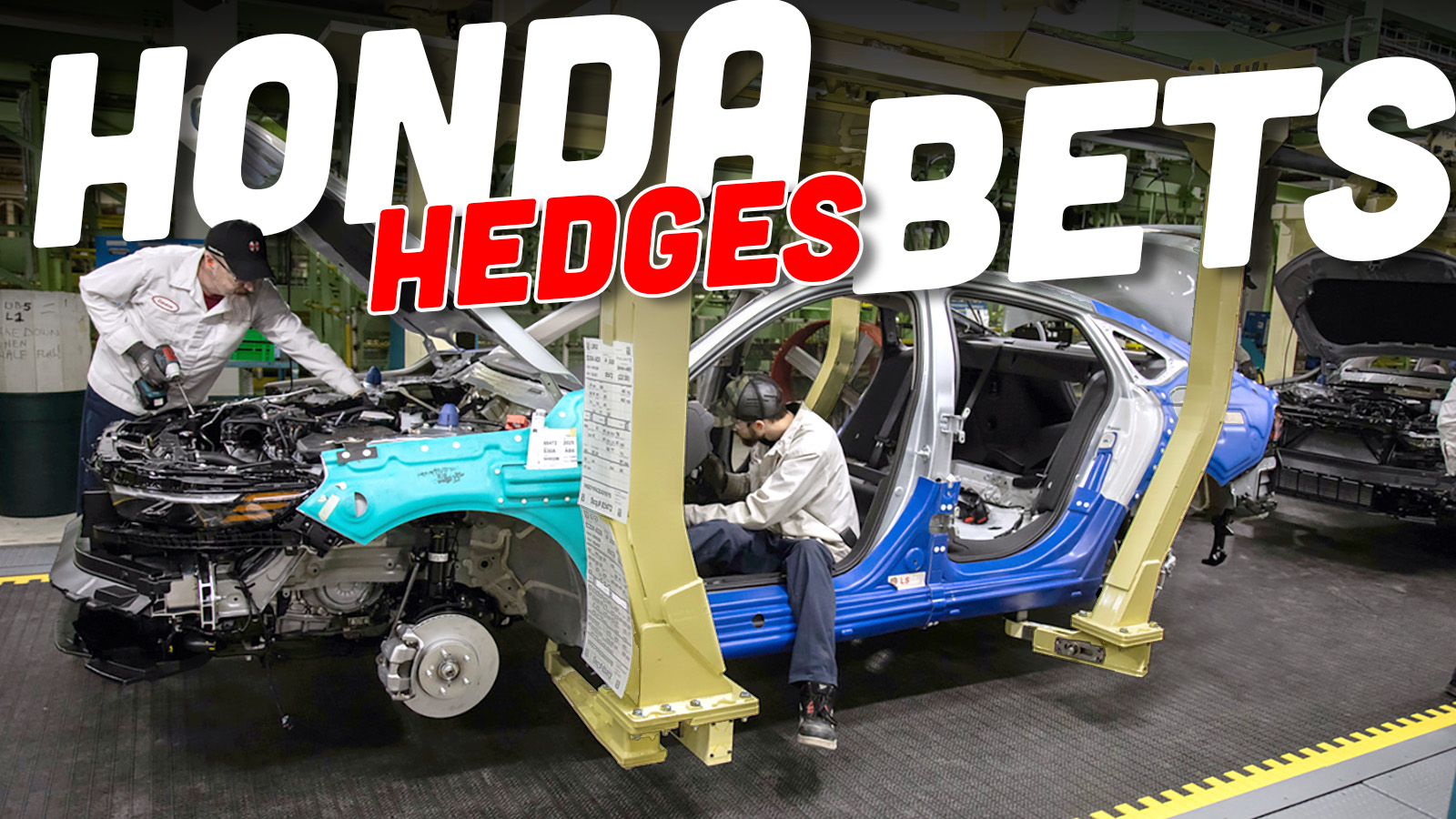
汽车行业正面临前所未有的挑战,尤其是在美国。全球大部分地区都决定转向低排放车辆,特别是电池驱动的车辆。尽管本田不像丰田那样热衷于电池电动车,但该公司仍然倾向于氢燃料电池技术。然而,本田正在扩大其BEV产品线,并最近邀请我参观其位于俄亥俄州中部的电动车中心。
本田在俄亥俄州拥有超过四十年的制造历史。1979年,该公司在哥伦布市附近的玛丽sville建立了第一个美国工厂,生产摩托车。三年后,本田成为第一个在日本以外开始在美国生产汽车的日本公司,并一直在此地生产雅阁和其他车型。
多年来,本田在俄亥俄州东利伯蒂和安娜又增加了组装工厂和发动机工厂。此外,该公司还在其他州和加拿大建立了生产各种产品(从动力设备到越野车再到喷气机)的工厂。
但构成“电动车中心”的是玛丽sville、东利伯蒂和安娜的工厂,以及位于俄亥俄州杰斐逊维尔的新电池工厂。这四个工厂将是北美本田电动车制造的核心。
杰斐逊维尔工厂是本田与LG能源解决方案的合资企业,计划每年生产高达40 GWh的锂离子电池(这足以装满约45万辆本田Prologue 85kWh电池组)。该工厂将生产类似于LG直接供应给本田或通过合资企业供应给其他汽车制造商(包括通用汽车、福特、大众集团、现代汽车集团、丰田、斯泰兰蒂斯等)的袋式电池。
杰斐逊维尔工厂还将组装这些电池模块。目前,本田对具体技术细节(如化学成分、容量或每个模块将包含多少电池)仍保持神秘,但在大多数其他使用案例中,通常每个模块包含约12个电池。
东利伯蒂工厂的年产能为24万辆汽车,目前生产CR-V和讴歌MDX、RDX。今年第四季度,东利伯蒂工厂还将开始生产索尼本田移动公司联合开发的Afeela 1,并正在进行一些调整以支持这一生产。
我们没有参观这两个工厂,但我们在玛丽sville和安娜的工厂度过了几天时间,了解这些工厂在过去一年中的变化。
玛丽sville是北美本田生产的最初所在地,目前是网络中产能最高的工厂,年产能为44万辆。它因其卓越的质量记录而闻名,1988年成为美国首个出口车辆(雅阁)的日本所有装配厂。玛丽sville也是本田研发的所在地,许多专门针对该市场的车型(包括奥德赛、普锐斯、帕特罗纳和几乎所有讴歌车型)都在这里设计和开发。
汽车生产是一个复杂且非常资本密集的过程。汽车由数千个单独的组件组成,这些组件来自数百家供应商,并需要在装配线上按正确的时间和顺序到达正确的站点。每个成功的汽车制造商都必须学习这一课。许多制造商仍在学习这一点,这也是许多有前途的初创公司失败的原因之一。本田多年来在这方面表现得尤为出色。
因此,当本田开始为在美国生产电动车做准备时,它必须做出一些艰难的决定。美国市场对电动车的接受速度不如欧洲和中国快,而且这里的政治让人们对插电式路径更加犹豫。在中国和欧洲,政府政策至少有一些更大的确定性。
因此,考虑到要花费数十亿美元来生产电动车,必须非常谨慎地决定要投入什么。本田一直比较保守,这一点在电动车项目中仍然适用(设计0系列车型是另一回事)。
本田没有像通用汽车那样拆除底特律-哈姆特拉克工厂,而是保留了建筑的大部分,也没有像福特那样在田纳西州建造一座全新的工厂,该工厂可能需要多年才能达到满负荷生产能力。本田继续采用灵活的生产方法。有趣的是,这并不包括放弃传统的转移装配线,而是安装了一套自动引导车辆(AGV)系统。
大多数本田装配工厂生产多种车型,车型大小和形状各异。许多本田产品也在多个工厂生产,以提供冗余,如果一个工厂出现问题,至少可以在其他地方继续部分生产。
玛丽sville目前生产雅阁、讴歌TLX和英菲尼迪。到2026年底,它将开始生产三个额外的车型:讴歌RSX、本田0 SUV和本田0轿车。自2025年1月起,预生产车型已经开始组装。本田没有中断其现有产品的生产。大多数国内品牌在进行此类转变时会关闭工厂长达一年或更长时间。本田定期执行代际车型变更,而最坏的情况也只是利用传统的夏季两周假期。
为了生产三款新电动车以及三款现有的使用四缸和六缸发动机、手动和自动变速箱以及混合动力的车型,本田决定将两条装配线合并为一条。
2023年,雅阁在U形装配线上组装,TLX和英菲尼迪则在第二条环绕雅阁线的装配线上组装。这使得零件到达站点变得复杂,导致狭窄的通道。2024年初,雅阁被转移到外讴歌线,然后开始拆除。
2024年2月至12月期间,旧雅阁线的一半被拆除,另一半更新以生产三款内燃机车型和三款电动车。讴歌线的转弯点处增加了一个新的环形,包括IPU安装站。IPU是本田的术语,通常称为电池组。
12月,第一条生产线与IPU安装环形连接,旧雅阁线的第二条生产线也与新的单线连接。在12月的假期停产期间,原始讴歌线的整个最终部分被拆除,混凝土地板也被更换。当我1月底参观工厂时,几乎看不到一个月前还在工作的装配线。
在访问当天,没有电动车正在组装,但我们看到了新的工作站,包括IPU环形。内燃机车型只需继续通过这一部分,无需额外工作。但当一辆电动车下线时,一个机器人系统会滑过来,将电池组抬起并放置到位,其他机器人则插入并拧紧固定电池组的螺栓,将其转变为车辆的结构部件。
生产线的更下游是一个新工作站,我们在参观工厂时正在安装。大多数现代车辆都有一些先进的驾驶辅助系统(ADAS),需要在安装时进行校准。目前本田和讴歌车型通常至少有一个前摄像头和长距离雷达,以及后角短距离雷达传感器。
本田计划在新电动车上提供至少无手驾驶功能,以及无手无眼的三级自动化系统。这将需要校准更多的全景摄像头和雷达传感器,甚至可能还需要一个面向前方的激光雷达。本田0轿车原型车包括一个顶置激光雷达。所有这些都需要在出厂前进行校准,因此在汽车进入最终滚测试之前,已经安装了一个更先进的校准室。虽然我们没有进入,但校准目标在室内外都清晰可见。
滚测试也在更新。这是大多数汽车装配线的标准功能。车辆被开上滚轮,启动,并进行一系列测试以确保变速箱换挡正常、刹车工作以及各种系统功能正常。这可以视为一次快速的厂内试驾。对于混合动力车型,他们还会测试前轮的再生制动,对于电动车,他们还会检查后轴的再生制动。
由于玛丽sville已经生产了多年的混合动力车型,工厂中已经有一部分区域专门用于准备那些相对较小的电池。然而,工厂的重新配置也腾出了空间用于IPU组装。电池外壳由安娜发动机工厂的压铸铝生产。与主要装配线不同,本田选择了AGV进行电池组装。
机器人用于将从杰斐逊维尔收到的模块安装到电池组中,并安装连接一切的汇流条。在模块进入之前,机器人会在模块所在的腔体底部涂抹热导膏,当模块插入并固定时,热导膏会被均匀分布,以提供从模块中移除热量的均匀接触面。
员工们安装较小的组件并连接一切。电池组被抬起并倾斜向工作人员,以方便操作和提高人体工程学。一旦所有组件都到位并连接好,盖子被拧紧,整个外壳进行泄漏测试,以确保不会有任何入侵。
有趣的是,所有组装好的电池组都装在托盘上,然后被装入拖车,而不是直接通过传送带运送到装配线。这允许暂时保留一到两天的库存,至少在电动车产量开始增加之前是这样。玛丽sville还为杰斐逊维尔工厂和东利伯蒂工厂进行电池组组装,后者将生产Afeela 1。拖车装载允许无论电池组在哪里使用,都能保持一致的产品。
在玛丽sville装配厂大约90分钟后,我们没有看到任何有趣的细节——叉车。出于安全原因,本田只使用叉车卸载零件拖车。在工厂内部,所有东西都装在手推车上,由牵引车拉到合适的站点。这使得司机有更好的视野,减少了事故的风险。
作为整体投资的一部分,本田还采取了多种措施以提高可持续性。工厂内的所有照明都已更换为LED灯,更节能,加热和冷却系统也已升级。
午餐后,我们驱车约45分钟前往安娜发动机厂,参观电池外壳的生产。安娜目前生产三种发动机:自然吸气的阿特金森循环2.0升四缸发动机,用于混合动力雅阁、思域和CR-V;2.0升涡轮增压发动机,用于思域Type-R和英菲尼迪Type-S;以及3.0升双涡轮V6发动机,用于讴歌MDX和TLX Type-S。
安娜工厂自1985年生产黄金翼摩托车发动机以来,规模不断扩大。目前占地280万平方英尺,每年生产110万台发动机。工厂内一直设有铝和铁铸造设施,能够生产许多主要部件,包括气缸头、气缸体、活塞、连杆、曲轴和CVT皮带。自成立以来,安娜已经生产了超过3000万台发动机。
作为电动车转型的一部分,一些组件制造已转移到其他地方,一些较旧的铸造设施已被淘汰。在现有南楼的空间内,本田正在安装其第一套大型铸造设备。
有人在参观时询问了大型铸造和巨型铸造之间的区别,以及哪种更好。现实情况是,它们都是营销术语,没有实际意义,就像“巨型工厂”也没有意义一样。巨型工厂和巨型铸造都是特斯拉创造的术语,旨在使工厂和过程显得更加特别。巨型/巨型铸造只是高压铝压铸大型部件。
在营销之外,本田正在安娜安装六台6000吨压铸机,其中五台已经到位,最后一台将在2月底安装。这些机器非常庞大,本田不得不在工厂侧墙上开一个16英尺×16英尺的门,以便机器能够进入。
这些机器成对安装,每对机器中的一台生产外壳的前半部分,另一台生产后半部分。本田多年来一直使用压铸工艺生产发动机缸体。然而,整个电池外壳宽1.3米,长近2米,是四缸缸体的四倍以上。零件越大,所需的压铸压力就越大,以确保零件均匀且材料不会在两个半模之间泄漏。
作为可持续发展的一部分,本田在多个领域进行了重点投资。他们开发了一种特定的铝合金,以提供所需的材料特性,保护电池,减轻重量,并且完全可回收。许多压铸合金不能简单地熔化再利用,它们实际上需要重新熔炼。本田使用的混合物允许废料、碎片和废料直接返回熔炉并重新进入生产过程。
高效率熔炉用于减少天然气消耗,并具有未来改造成等离子弧焊接的能力,以进一步减少排放。喷在模具上的润滑剂以允许零件分离的量也保持在最低限度。在后续的加工过程中,本田使用最小量润滑剂工艺。这种方法允许润滑剂在加工过程中蒸发,留下干燥的切屑,可以直接压缩回熔炉。
当铸件从模具中出来时,它们直接进入淬火槽约8秒。这种材料组合和直接从模具到淬火的组合消除了单独热处理过程的需要,这是金属部件生产中最耗能的部分,也是产生最多二氧化碳排放的部分。另一个主要优势是热处理往往会导致零件变形,进而需要更多的加工,增加成本、能源使用和排放。
淬火后,机器人将铸件放入另一台机器中,切掉溢流和浇口,这些是铝注入的地方。
由于铸件的尺寸,它被分成两半铸造。如果一次性铸造,将需要一个更大尺寸的铸造机和更高的压力。将铸件分成两半也提供了不同车型的灵活性。目前所有铸件都使用一个共同的前半部分,有两个不同的后部分,以适应13模块电池或更大的16模块单元。
铸造后,在生产线的末端,铸件通过光谱测量机。在第一阶段,90个摄像头拍摄数千帧,这些帧被缝合在一起,形成一个精确的三维模型,超过1200个检查点确保铸件在铸造过程中尺寸正确且平坦。整个过程大约需要30秒,比使用坐标测量机进行相同任务所需的时间更准确。这种更快的循环时间允许100%的零件检查。同样,完成的铸件通过另一台具有120个摄像头的光谱测量机进行分析。
在两部分加工后,它们需要连接。本田使用摩擦搅拌焊接,这是一种工艺,其中旋转头沿着部件之间的接缝移动,使材料部分熔化成塑料状态并融合成一个整体。与许多其他工艺一样,这比传统焊接工艺更节能,没有火花或其他残留物。
最后的阶段是添加冷却板。这是安娜第一次从玛丽sville提供组件。玛丽sville的车身冲压车间生产冷却板,摩擦搅拌焊接用于将板连接到电池外壳的底部。在操作过程中,冷却液通过板和铝外壳之间的通道管理电池温度。
鉴于美国对电动车的采用存在不确定性以及建立任何车型所需的资本成本,确保最大限度地利用现有设备绝对是明智的。当然,其中一些投资是专门用于电动车,尤其是电池生产。但拥有一个可以容纳从100%内燃机到100%电动车的装配过程,是未来几年的正确答案。
我们将等待本田电动车平台的技术细节,以确定他们是否能够利用不使用多能源架构的优势。纯电动车可以比灵活架构更简单、更轻,并且具有更好的包装。本田似乎已经将一些元素融入其设计中,以在制造可制造性方面做出更好的妥协,同时保持一些电动车架构的好处。
本田电动车中心的工作似乎是最合适的方向。希望从玛丽sville出来的车辆(尽管Afeela 1与本田和讴歌电动车共享许多组件,我对它持保留态度)值得这一努力。
“`(编辑:卖车180小义)
如果您现在或者未来有卖车计划,可以点击“卖车180”或者扫描下面的微信公众号,卖车180,又快又高价。
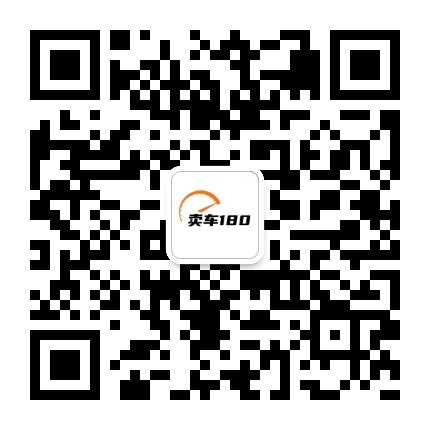